Sheet Metal is the most widely used engineering material. Sheet metal parts & Components are drawn or made from variety of materials like Steel, Aluminum, Copper, Brass.
It is versatile and is used in various applications, including industrial and manufacturing.
At UMS we have modern machines, experienced human resources, qualified, experienced and award-winning engineers to cater to any metal forming and working technology.
We expertise in providing sheet metal solution to Automobile, Electronic & Electrical, Hydraulic, Pumps, Motors and other Industries.
Process Engineering
ENGINEERING EXPERTISE FOR COST EFFECTIVE PRODUCTS: UMS Enggering excel in Precision Machining processes like Turning, Milling, Grinding, Specialty Metal Removal and Super Finishing, utilizing both Conventional and Advanced CNC Machines. Our expertise lies in optimizing process-machine combinations for optimal Cost, Precision, Volume, and Time efficiency benefits for us and our clients.
VALUE ENGG, REVERSE INTEGRATION & DESIGN UPGRADE: For every job UMS undertake, we reassess design parameters and provide optimal manufacturing ability solutions. Drawing upon our expertise in backward integration and value engineering, we propose alternative raw materials, cost-effective processes, suggest tolerance revisions, adjust surface finishes / fits & minimize machining allowances & wastage.
HANDLING INTRICATE AND ADVANCED JOBS: We handle parts / components having intricate shapes & profiles. We handle machining & super finishing of components with close tolerances and geometric accuracy on various types of Ferrous, Non-Ferrous & other non-metallic raw materials like Plastics & Hard Polymers.
MANUFACTURING ENGINEERING & TOOLING SOLUTIONS: Our team is experienced in manufacturing engineering, tool design / development and preventive maintenance systems supported by tool room for jigs, fixtures, work holding devices and special inspection gauges etc. We help our clients achieve mass production with consistent quality at minimal inspection, which is time critical and cost effective.
ALLIED PROCESSES, ASSEMBLY ENGG. & TOTAL SOLUTIONS: We are total solution provider to our clients. Post-manufacturing, we provide supportive activities like surface treatment, electroplating, heat treatment, other allied processes & assembling, customized packaging and choosing dispatch partner who is efficient in delivery.
Manufacturing
The raw materials we use are of various International Standards like DIN, BS, ASTM, EN, JIS, ISI, etc for ferrous & non-ferrous metals.
Non-Ferrous Metals like Copper, Brass & Other Copper Alloys, Aluminum Alloys
Ferrous Metals like Carbon Steels Alloy Steels Stainless Steels
Hard Materials like Plastics & Polymers Phenolic Materials Fiber Glass
Input Forms Utilized: Bar Stocks (Rounds, Squares, Flats & Profiles), Tubes & Pipes, Blocks & Thick Sections, Forgings & Castings
As a part of our total solutions approach, we offer auxiliary and allied processes encompassing
Heat Treatments: Conventional Hardening and Tempering / Annealing, Case Carburizing / Hardening, Induction Hardening, Plasma Nitriding et
Surface Finishing: Polishing, Buffing, Etching, Laser Etching and Electro Polishing
Surface Plating / Coatings: Zinc Plating, Nickel Plating, Black oxidizing, Powder Coating & anodizing in different Qualities / Colors etc
Specialty Surface Plating / Coatings: Hard Chrome Plating, Silver & Tin Plating, Electrolysis Nickel, etc
All our products are manufactured in adherence to our quality policy & work system manuals. Please visit our quality page & work manuals for an in depth understanding of our procedures & systems. Additionally, quality procedures specific to our precision machined components manufacturing are…
Typical testing & inspections inclusive of raw material testing for chemical composition and physical properties, surface roughness testing, ultrasonic testing, dye penetrant testing, etc as per clients’ drawing / specification Customized & comprehensive quality tests are as per client drawings / specifications using precisely designed and developed inspection gauges and devices.
We are committed to understanding our customers’ requirements in order to provide them with suitable, high-quality solutions. Our products and solutions are designed to help our customers succeed in the market.
We believe the key contributors to customer delight and quality product are the employees, right processes & procedures, right machines, tools & equipment and management participation.
Our team of expert specify the steps, phases and actions required to perform the process. Our management team ensures right team and experienced people are selected for an assignment. The team lead is responsible for giving the working instructions & procedures to be followed, The worker knows, what is required to do be done in his everyday tasks. We nurture people of quality by continuous education and training. We explain them the importance of the parts or the component produced.
Employees are provided with the right machines, tools & equipment to support quality product delivery.
We continuously strive towards process improvement. Our quality policy sets out the framework for our quality objectives and is regularly reviewed to makes sure that it is still adequate and fit for purpose.
Achievements
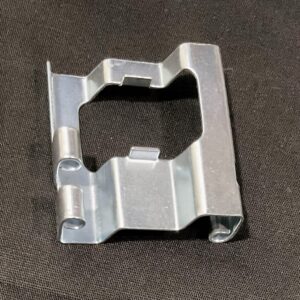
Product Name: Roller Cage LH
Application in Industry: Automotive
Material & It's Forms: CR-DD AS PER IS 513-2016
Product Dimensions:
- Maintain CC parameter within 0.05
- Maintain close tolerance as per customer requirements.
Design Intricacy: ROLLER CAGE is difficult part because of it's leg bending in opposite direction with minimum curling gap. Major challenge was to maintain ID as per customer requirements.
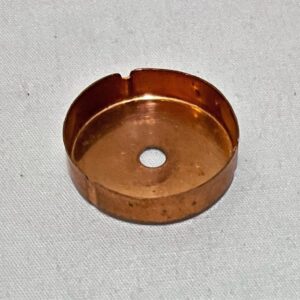
Product Name: Copper Support Cap
Application in Industry:
Electrical and Electronics.
Material & It's Forms: Electro-Copper.
Product Dimensions:
- Maintain CC parameter within 0.05
- Maintain close tolerance as per customer requirements.
Design Intricacy:
Achieved all parameter within 0.05 mm OD Height etc. and ID within 0.02 mm.
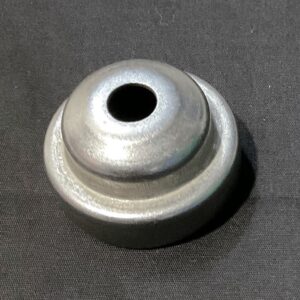
Product Name: Dust Cover Cap
Application in Industry:
Automotive.
Material & It's Forms: CR-EDD AS PER IS 513-2016.
Product Dimensions:
- Maintain CC parameter within 0.05
- Maintain close tolerance as per customer requirements.
Design Intricacy: Draw height is more than 24 mm and it will be maintained within 0.4 mm in press tool. Maintain thinning within 1.20 mm for 1.50 mm material.